Marine heat exchangers play an important role of removing the heat produced by a running machinery to ensure smooth functioning of the equipment. It is also necessary to enhance the heat exchanging ability which would reduce after certain amount of time of operation.
The cooling medium used in the heat exchanger depends on the medium used, including other factors.
Along with mediums such as fresh water, air and oil, sea water is also used abundantly in marine heat exchangers as an important cooling source. However, because of the presence of dissolved salts in sea water, corrosion and scale deposits is a common condition in heat exchangers. Maintenance of marine heat exchangers is therefore necessary at regular intervals of time to prevent reduction of heat transfer or failure of equipment.
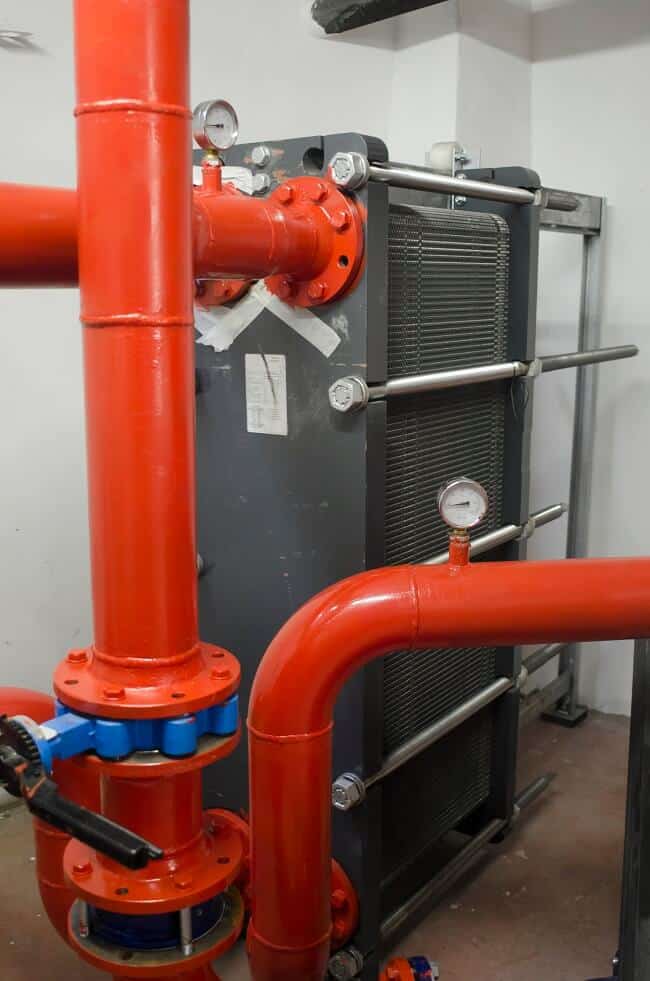
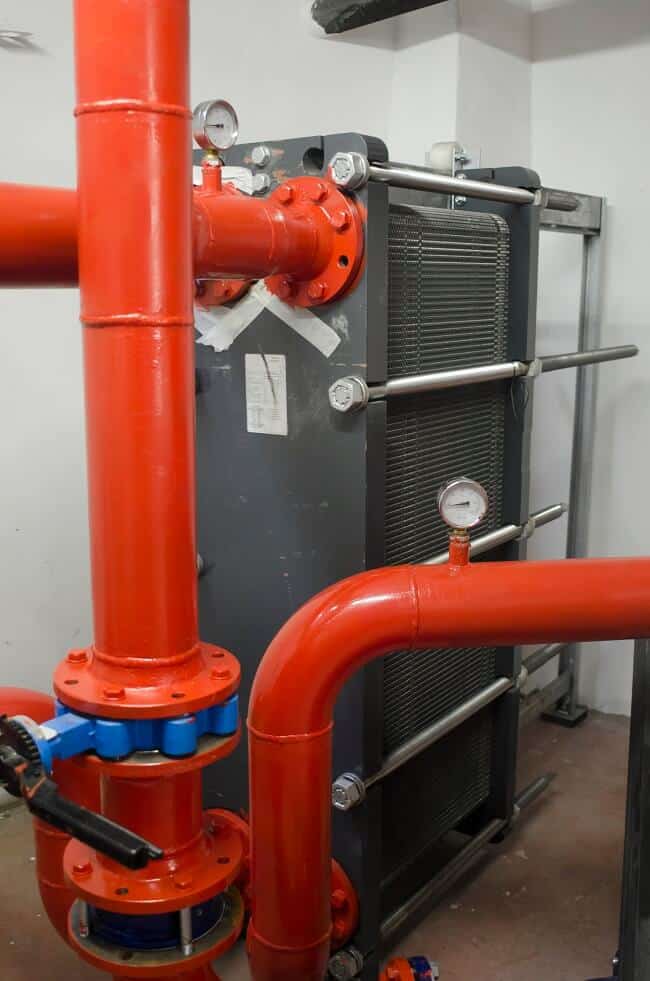
The method of maintenance used depends on the type of heat exchanger and type of deposits, but the general aim of every heat exchanger maintenance procedure remains the same – cleaning of heat transfer surfaces to prevent any kind of obstruction in the flow process.
The main reason for fouling of heat exchanger surface is the increase in temperature difference between the two fluids and change in pressure. But it is the sea water side of the heat exchanger which suffers the most as a result of corrosion and scale deposits.
Methods of marine heat exchanger maintenance
Note: Prior to Maintenance, isolate the heat exchanger by shutting off the line valves for both medium and media; and drain the remaining liquid using the drain cock. The Vent must be open to ensure everything is drained from the heat exchanger.
- If the deposits on the heat exchanger are not so hard, then they can be removed using a wire brush.
- If the deposits are stubborn, chemical cleaning should be used by emersion of the part in chemical solution.
- Depending on the type of the heat exchanger, there are tools provided by the manufacturers for the cleaning purpose. For e.g. there are special tools for cleaning shell and tube type heat exchangers.
- Once the cleaning is done, the heat exchanger must be flushed with fresh water to remove any remaining chemical or dirt from the surface.
- In sea water cooled heat exchanger, anodes are fitted on the cover to prevent it from galvanic corrosion. Anodes must be checked and changed if required.
- Always renew the cover gasket if it is damaged during opening of heat exchanger.
- In oil coolers and heaters, fouling can take place on the outside of the tubes as well. This can be removed by chemical flushing.
In plate type heat exchangers, the stack of plates is removed to expose the surface. The plate surface is then cleaned with brush or by the methods suggested by the manufacturer. (Sharp tools should be avoided). Cleaning should be done in such a way that it does not damage the plate seals. However, if a replacement of the seal is necessary, it must be done before putting the plates back.
While tightening the plates together, care must be taken for even tightening of all the exchanger studs and bolts or else leak will occur.
Excessive corrosion of the heat exchanger surface can also lead to perforation of the surface, resulting in mixing of one liquid with another. Minor leakage detection is not easy especially when the header tanks are automatically toped or if there is no proper manual record maintained. However, major leakages can be easily detected as a result of sudden loss of lubricating oil or jacket water. Low level alarms are also useful in detecting major leaks.
Another way to prevent mixing of two liquids because of perforation is by keeping the sea water at a pressure lower than the jacket water or any other liquid used. This reduces the risk of sea water entering into other mediums.
How leaks are detected?
Shell and tube type heat exchangers
If it’s a shell and tube type heat exchanger, leaks can be detected by following the procedure below:
Isolating the heat exchanger from the system and draining the sea water
Removing the end covers or headers to expose the tubes or plates
If the surface is clean and dry, inspection of the liquid flow is made from around the tube ends and through the perforations. However, in large coolers it is difficult to get the coolers extremely dry to visualize any perforation. In such cases special fluorescent dye is added to the shell side of the cooler. The dye glows when an ultraviolet light is shone on the tube, revealing the tube leaks.
Plate Type Heat Exchangers
Similarly in plate type heat exchangers, visual inspection or fluorescent dye penetrate is used to find any defeats. (Dye penetrate is used on one side, followed by ultraviolet rays on the other side)
Air coolers
When it comes to air coolers, leakages can be dangerous as they allow sea water to pass through to the engine cylinder. This can lead to formation of scales on air inlet valves’ spindle.
In such cases, location of the leaks can be detected by allowing low air pressure on the air side and checking the flooded sea water side for air bubbles. For better results, soapy water can be used for sea water side flooding.
Apart from the above mentioned methods, there are other ways as well to carry of marine heat exchanger maintenance. However, these are the most commonly used ones.
Do you know any other ways? Please explain them in the comments below.